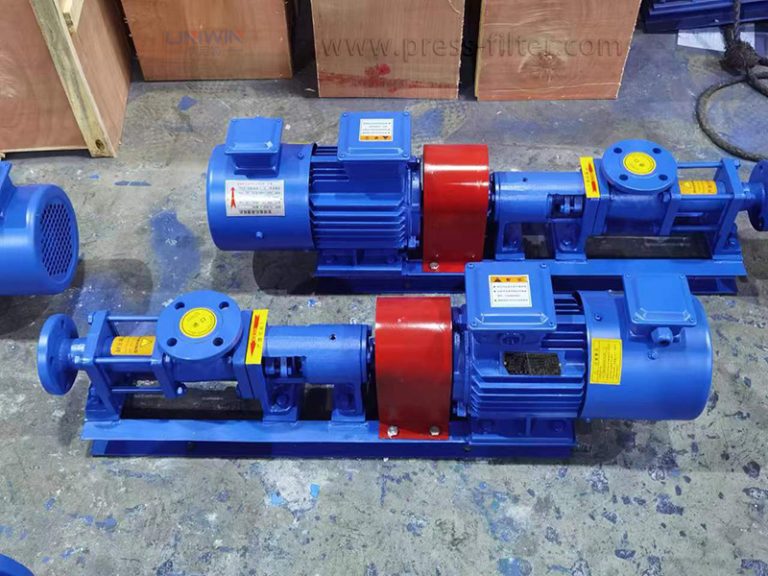
Single Screw Pump for Filter Press
The G-type single screw pump often operates based on the rotary meshing volumetric principle. Unlike typical pumps, the G-type single-screw
♦A filter press pump is a type of pump used in conjunction with a filter press, which is a device designed for separating solids from liquids. Filter presses are commonly used in various industries, including wastewater treatment, chemical processing, mining, and food production.
♦The filter press pump plays a crucial role in the operation of a filter press by facilitating the movement of the slurry, into the filter press chambers. These pumps are designed to generate the necessary pressure to force the slurry through a series of filter plates or cloths within the filter press, separating the solids from the liquid.
♦Filter press pumps can come in various types, such as diaphragm pumps, centrifugal pumps, or plunger pumps. The choice of pump type depends on the specific requirements of the filtration process, including the characteristics of the slurry, the desired flow rate, and the pressure needed to achieve effective separation.
The G-type single screw pump often operates based on the rotary meshing volumetric principle. Unlike typical pumps, the G-type single-screw
Dosing pump, also known as metering pump, is a commonly used equipment in filter presses and is usually used in
QBY series pneumatic diaphragm pump is a new type of conveying machinery and a novel type of pump in China.Especially
The CDLF series is a lightweight vertical stainless steel multi-stage centrifugal pump, innovatively designed by integrating both domestic and international
The ISW-type horizontal centrifugal pump, often utilized in filter press applications, is crafted from the unique structural amalgamation of the
The IH-type stainless steel chemical centrifugal pump, often integrated with filter press systems, is a single-stage, single-suction cantilever design. This
The QBY series pneumatic diaphragm pump uses compressed air as the power source and can pump all corrosive liquids. It is one of the most commonly used pumps for filter presses.
There is no need for irrigation and water diversion, and the flow is wide. It can not only pump flowing liquids, but also transport some non-flowing media. This pump does not need to be lubricated with oil. Even if it is idling, it will not have any impact on the pump. The lift and flow rate can be adjusted steplessly through the opening of the air valve. The standard suction lift is up to 7m, the head is up to 50m, and the outlet pressure is ≥6kgf/c㎡.
The G-type single screw pump is an internally meshed closed screw pump, which is a rotor-type positive displacement pump. The pump has strong adaptability to the medium, stable flow, small pressure pulsation, and high self-priming capacity.
It is widely used in filter presses and can transport media with high solid content and transport sensitive items and items easily damaged by centrifugal force.
Vertical multi-stage centrifugal pump is also called CDLF vertical multi-stage centrifugal pump , it’s particularly suitable for filter press applications.
Without changing the installation area, the head can be increased or decreased according to the needs of the pump stages and the outer diameter of the impeller, meeting the needs of different actual situations. . The flow-passing parts of the pump are made of stainless steel (304\316) and can be used in mildly corrosive media.
How To Select The Feed Pump of Filter Press
The most common feed pumps include Centrifugal Pump, Screw Pump, Diaphragm Pump, Plunger Pump, etc. At present, centrifugal pumps are the most widely used in industry, including ordinary pumps, stainless steel pumps, mud pumps, slurry pumps, corrosion-resistant plastic pumps, etc.
1.Flow Rate: Determine the required flow rate to ensure the filter press can operate efficiently. It should match the filter press’s capacity and the desired filtration speed.
2.Pressure: Select a pump that can generate the necessary pressure to force the slurry through the filter cloth and achieve proper dewatering.
3.Material Compatibility: Ensure the pump materials are compatible with the slurry being processed, as some fluids may be corrosive or abrasive.
Maintenance: Select a pump that is easy to maintain and service.
4.Consult with an Expert: If in doubt, consult with a pump expert or filter press manufacturer to ensure you choose the right pump for your specific application.
1. The inlet pressure should not exceed the maximum allowable operating pressure of the pump.
2. Ensure that the pump pressure pipeline system can withstand the highest output pressure achieved and ensure the cleanliness and normal working conditions of the drive air system.
3. Ensure that the largest particles contained in the fluid do not exceed the maximum safe passing particle diameter standard of the pump.
4. Do not point the exhaust outlet towards the work area or people to avoid personal injury.
5. Fasten the pump and each connecting pipe joint to prevent static sparks caused by vibration, impact and friction. Use antistatic hose.
6. Periodically check and test the reliability of the grounding system, and the grounding resistance is required to be less than 100 ohms.
1. The pneumatic diaphragm pump uses compressed air as power to complete the work. In this process, no electricity is needed, which also reduces accidents caused by electric shock. Therefore, the safety of pneumatic diaphragm pump will be better.
2. The working power of the screw pump is electricity, so during the working process, a certain amount of heat will be generated due to friction.
3. Compared with the two, the screw pump has a strong ability to transport abrasive fluids. Both have the advantage of taking up less floor space. However, diaphragm pumps produce significant vibrations that propagate through the pipeline, causing pipeline and infrastructure vibrations. Vibration damping devices are almost always installed together with diaphragm pumps. Their failure, jamming, inaccurate positioning, etc. can cause problems in the entire system. However, screw pumps are vibration-free and operate smoothly and quietly.
When the pump is running, if for some reason the absolute pressure of the pumped liquid drops to the vaporization pressure of the liquid at the current temperature in the local area of the overflow part, the liquid will begin to vaporize there, generating a large amount of steam and forming bubbles.
Copyright © 2023 China Uniwin Filter Press | All Rights Reserved.